22-year-old Fendt Favorit 515C gets £15k revamp
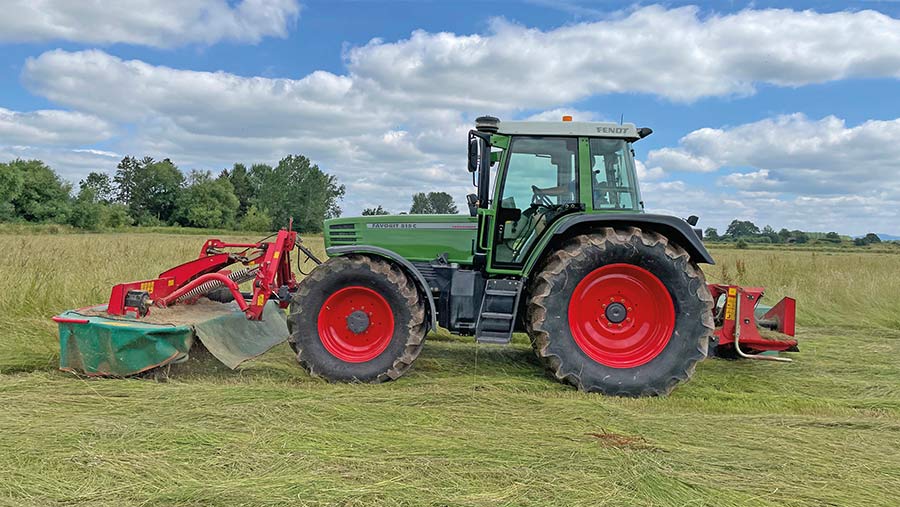
The allure of a new, top-spec tractor might win over many farmers and contractors, but Matthew Barnett has considerably more time for older machines with a proven track record.
He operates a fleet of five Fendts on his 285ha farm and apple-picking business near Hereford, and his favourites are the earlier models that hail from the late 1990s/early 2000s.
The reason is that these tractors are recent enough to have the power and features to rival a modern alternative, without the complex electronics and emissions paraphernalia that can prove tricky and expensive to fix.
Mr Barnett spent a lot of time driving Fendts of this era when he worked for a local potato grower, and they stood out for the level of driver comfort and high-end equipment, most of which came as standard.
“They had 50kph transmissions, air brakes, adjustable front-axle suspension, a turbo-clutch and the option of a front linkage and pto. Nothing else could touch them at the time and they still stand up well against new models,” he says.
See also: Video: Fendt Vario 516 on test
Machinery fleet
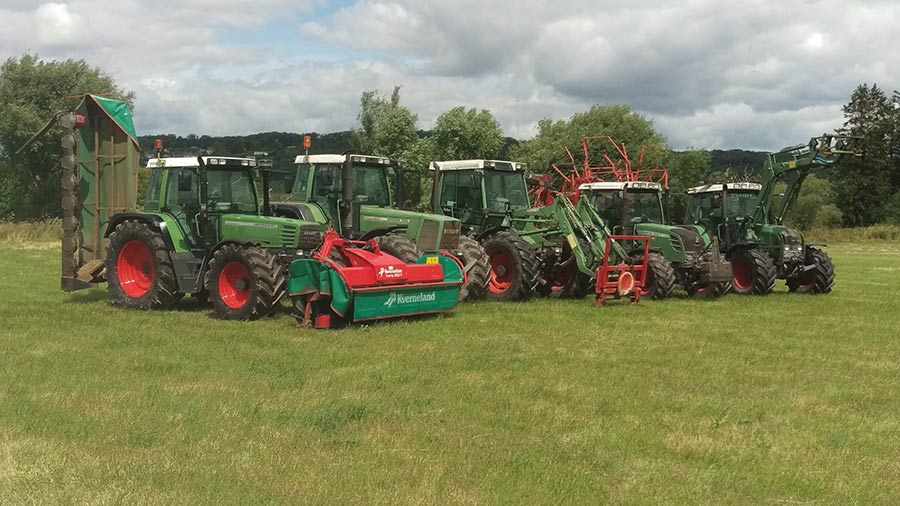
© MAG/James Andrews
- Tractors: 1999 Fendt Favorit 515C, 2000 Fendt 924, 1994 Xylon, 2008 312 Vario, 2005 412 Vario, Deutz-Fahr 430TTV
- Telehandlers: 2006 Merlo 3610 x 2, 1998 and 2003 Caterpillar TH62
- Grass kit: Kverneland 2832 front and 2632 rear mowers, Kverneland 8480 eight-rotor tedder, Kuhn 8121 two-rotor rake
- Drills: 4m Vaderstad Rapid, 3m Simba Mini Flow
- Cultivation kit: Dowdeswell five-furrow plough, 3m Maschio power harrow, Simba Top Tillth
- Apple equipment: MRB self-propelled harvesters x 3, MRB apple tree shakers x 2, MRB apple cleaner loaders x 2, MRB two-row tree planter
- Diggers: 13t and 8t Kobelco, 2.8t Hitachi
- Trailers: 12t and 16t root trailers x 4, 28ft MRB bale trailer, 28ft MRB low loader
Favorit 515C
The prized member of his collection is a 1999 Favorit 515C that’s just been treated to a major restoration.
This involved stripping it down to the chassis, fixing any mechanical problems, repainting all the surfaces and refurbishing the interior.
The tractor came into Mr Barnett’s ownership seven years ago, after he purchased it from a local contractor for £20,000.
It had only worked 6,000 hours and was mechanically sound, but the bodywork was a little rough.
“It’s hard to find 515s that aren’t on silly hours, and I’d been running a couple of well-worked 512s while I kept my eye out for a good one. I knew the cosmetics could be sorted, so I decided to buy it.”
Sitting on a T registration plate, this tractor is one of the last 515s produced – before the 700 Varios were introduced – and it comes with a high factory spec, including a front linkage and pto, loader brackets and mid-mount spools.
This makes it ideal for powering a set of front-and-rear mowers and being fitted with a front-end loader.
Keen to keep the tractor original, Mr Barnett also went in search of a factory Cargo loader that would slot straight into the brackets.
These have the benefit of plumbing into the mid-mount spools, which are operated via a joystick in the cab.
After a considerable amount of searching, he eventually managed to track one down through dealer PHR in Essex, which set him back £3,000.
The tractor was put straight to work with the plan to give it some cosmetic tidying if it turned out to be a keeper.
As it has a 6.2-litre, six-cylinder MWM engine developing 150hp as standard, the tractor spent most of the spring and summer season powering a set of Kverneland 6m front-and-rear mowers.
The combination of a six-range, four-powershift gearbox with “turbo-clutch” also meant the tractor was well suited to loader work.
This clutch was a precursor to the brake-to-neutral function used on modern semi-powershift tractors and means the 515 can be brought to a standstill by standing on the brakes without dipping the clutch pedal.
It also comes into its own when pulling up to junctions on the road, says Mr Barnett.
“Its only downfall is the dry rear brake setup, and if it weren’t for the front prop shaft brake it would be a nightmare to bring to a stop,” he says.
Over the next few years, the tractor racked up another 2,000 hours – putting it on a total of 8,000 – during which it succumbed to a few mechanical breakdowns.
These included the turbo-clutch assembly, which failed shortly after he got it, and the idler bearings in the hydraulic pump.
“When you’re running older tractors, you’ve got to accept that they’re going to break down now and then. However, they’re not usually that expensive to fix and the lower purchase cost means you can afford to have the odd spare knocking around,” he says.
“I’m not a fan of swapping implements around either, so I like to have a few tractors hooked to machines that I can just hop on and drive.”
The last breakdown was the main clutch and Mr Barnett sent the tractor to his friend, independent mechanic and tractor restorer Steve Hodges, for repair.
While it was there, he decided it was time to have some of the tractor’s cosmetic disfigurements tidied up too.
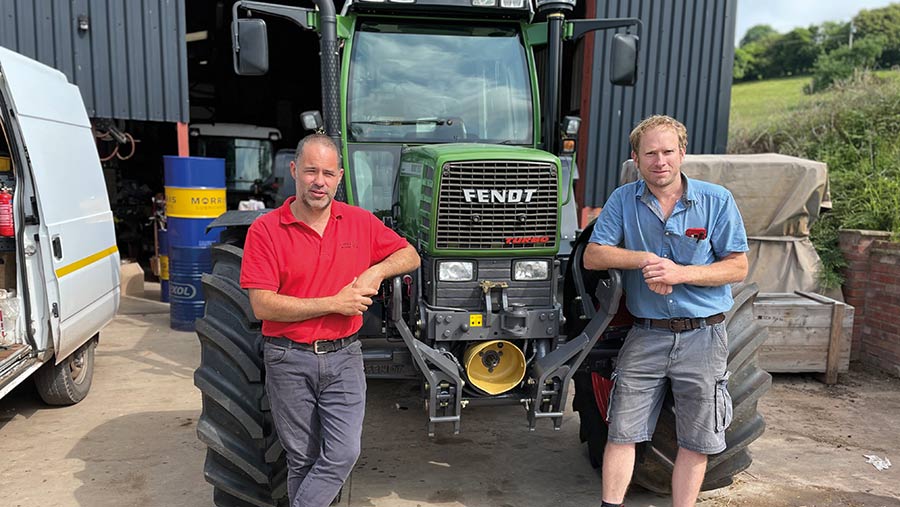
Restorer Steve Hodges (left) and owner Matthew Barnett © MAG/James Andrews
“That’s when things got a bit carried away – I only intended to get a few jobs done, but once the tractor was in bits, I changed my mind and decided to do it properly.”
All in, the restoration job cost just over £15,000 – a paltry sum compared to that required to upgrade to a new model.
It puts his total outlay for the tractor at about £35,000, which he would likely recoup were he to sell it.
The tractor has since gone back to work, with its primary job carrying out about 180ha of mowing to produce forage for the farm’s suckler herd and to sell on.
Although the MWM engine’s 150hp was ample for most jobs, it was a little flat compared to the 512s he had before, both of which were tweaked.
Mr Hodges turned the screw on the pump so that it was putting out roughly 147hp on the dyno, which he reckons equates to an engine power of about 160hp.
Mr Barnett says it has made a significant difference to the tractor’s performance. “It flies up the banks now and I can cruise along with the mowers at 17kph if I want to.”
The 515 will also be used with its Cargo loader (yet to be restored) but it won’t be one of the primary materials handlers.
“It’s still going to clock up plenty of hours, but I don’t want to knock it about on rough work as Steve has made such a good job of it,” he says.
His plan is to keep the 515 indefinitely and he hopes to be able to give his year 2000 924 Vario and 1994 Xylon the same treatment in the future.
Restoration process
The 515 arrives at Steve Hodges’ workshop near Bromyard, Herefordshire in its working clothes. It’s in sound mechanical order – other than a failed main clutch – but the years haven’t been kind to the bodywork and paint finish.
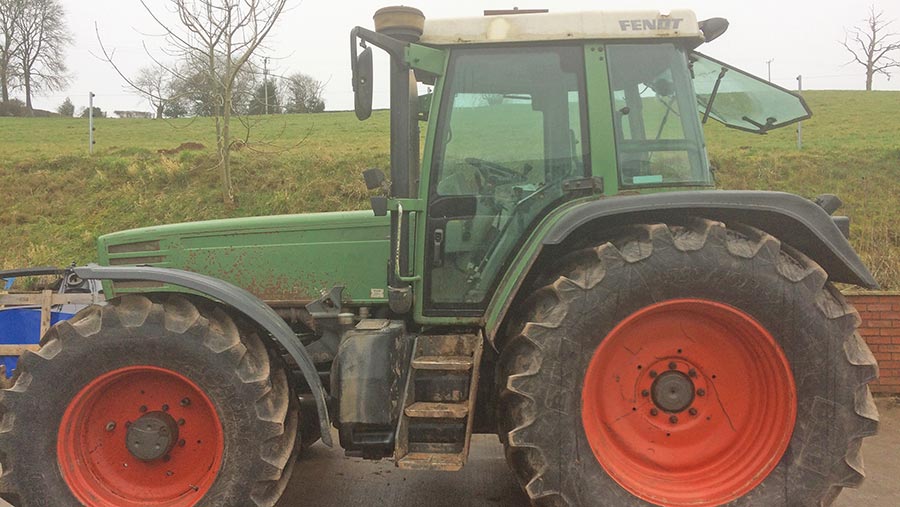
© MAG/James Andrews
The strip down begins, removing all body panels, the cab frame, floor and fender assembly to reveal caked-on crud and corrosion.
All ancillary items that are practical to take off are removed, but the wiring looms and hydraulic pipes are left in place.
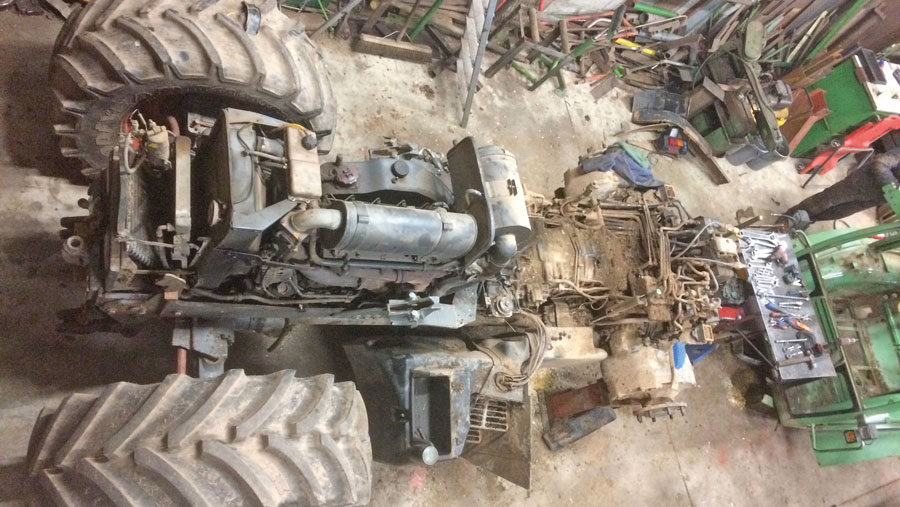
© MAG/James Andrews
The exposed chassis is given a thorough clean before the painstaking job of prepping it for painting takes place.
While the tractor is this easy to work on, Mr Hodges replaces the main drive clutch (a £1,000 part), fixes some back-end oil leaks and swaps any worn pins and bushes.
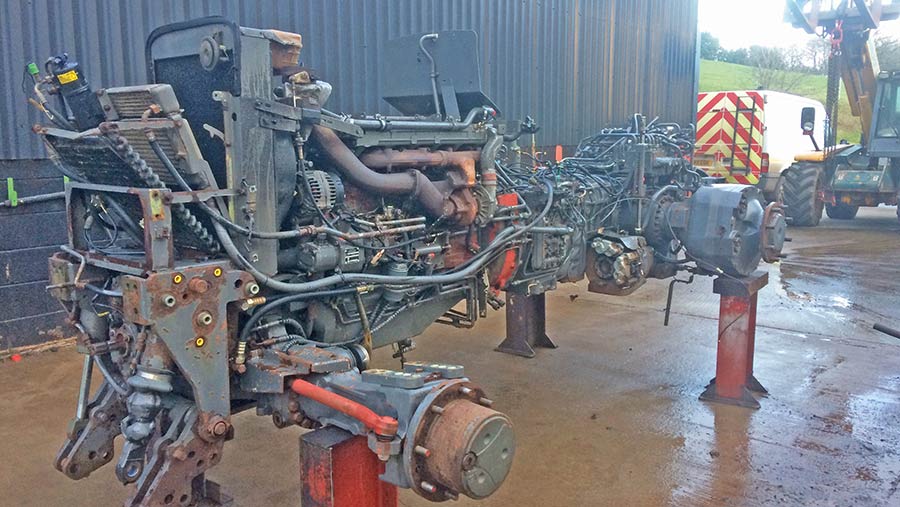
© MAG/James Andrews
Rot has taken hold in some sections of the cab frame, so the worst areas have new metal welded in, and more superficial patches are rubbed down and treated to prevent it coming back.
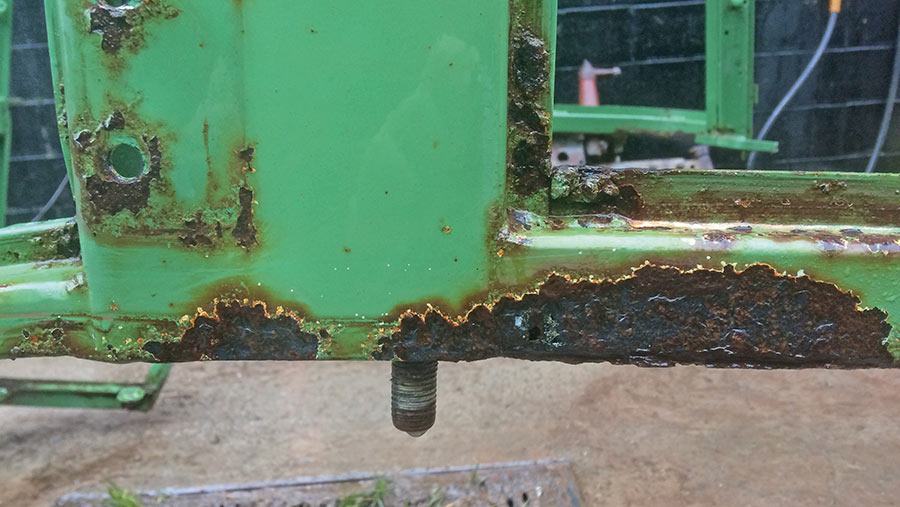
© MAG/James Andrews
The cab frame, roof section and body panels are sent for shot blasting before making their way to a local car body shop for a professional respray.
The prepped cab frame and all body panels are primed and sprayed with a two-pack paint finish in factory-correct Fendt green.
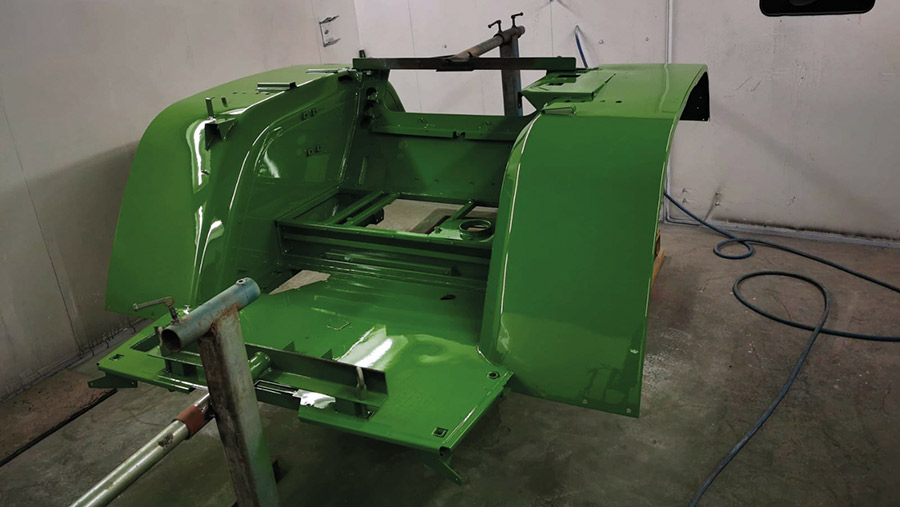
© MAG/James Andrews
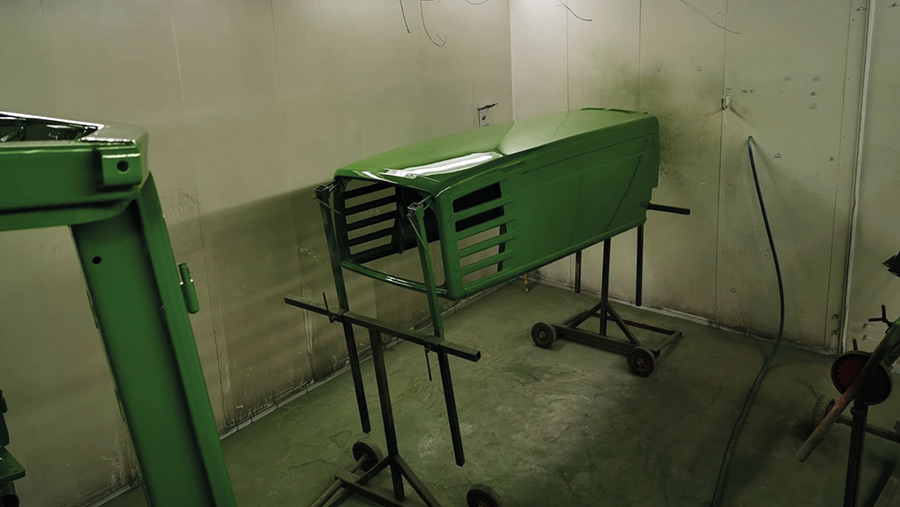
© MAG/James Andrews
Mr Hodges applies two-pack grey paint to all sections of the chassis, the engine and ancillaries.
Removable items, such as the pick-up hitch, rear linkage and air tanks are painted separately to give a better finish.
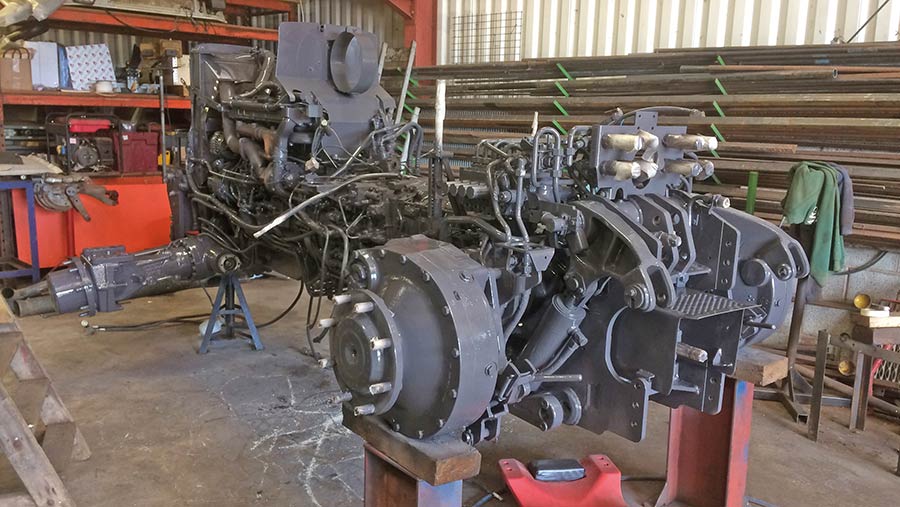
© MAG/James Andrews
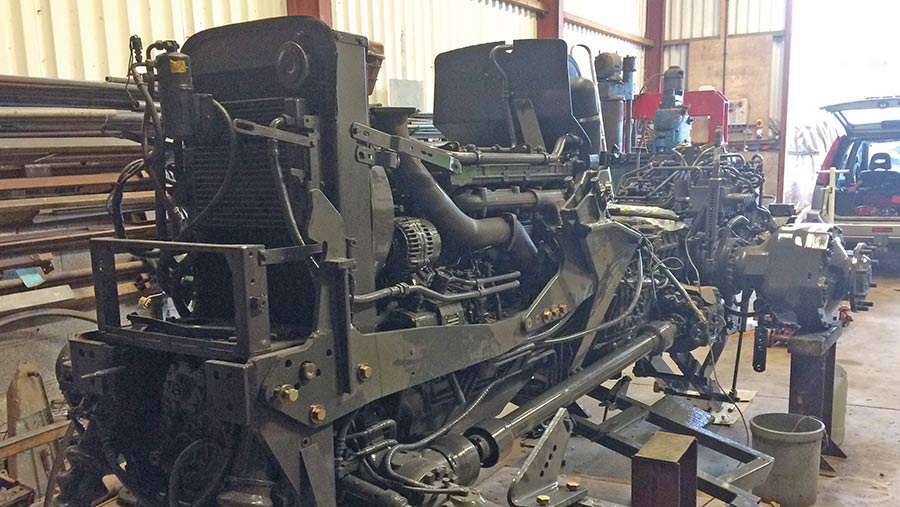
© MAG/James Andrews
Re-assembly gets under way, and with the refurbished cab frame slotted into position, it’s starting to look like a tractor again.
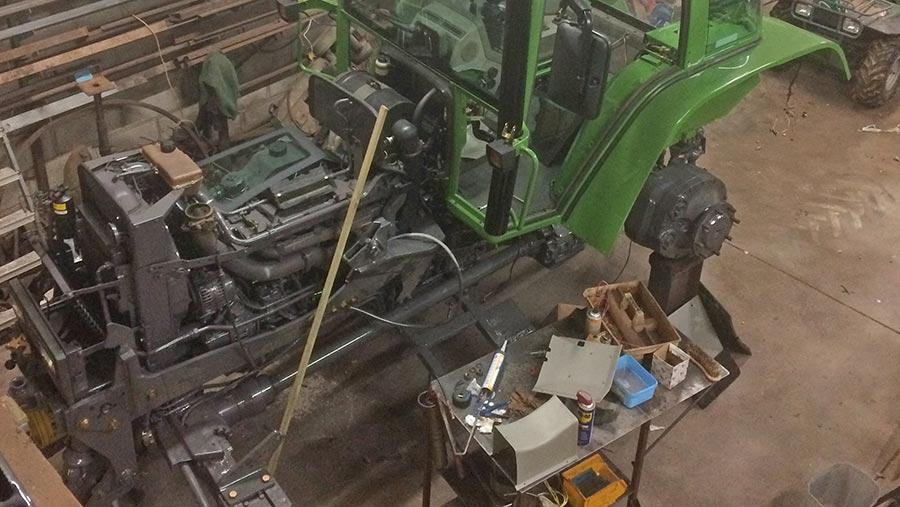
© MAG/James Andrews
To give it the new tractor look, all the nuts, bolts, screws and brackets are sent to a local firm to be re-plated.
This process involves dipping them in acid, before electroplating them with a protective layer of yellow zinc, just like the finish Fendt used originally.
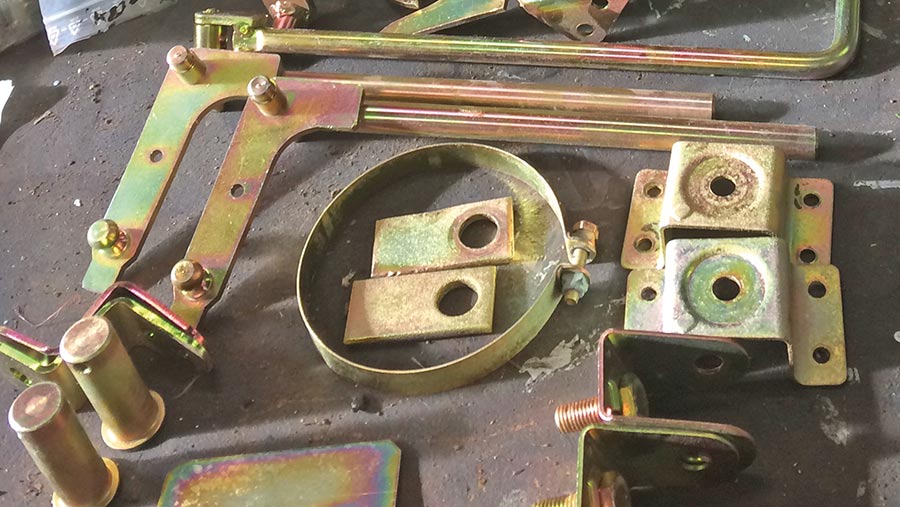
© MAG/James Andrews
The cab interior is put back together and grubby pieces of trim are given a thorough clean.
Any damaged sections are replaced where it’s economical to do so, which rules out the £500 cracked left mudguard trim panel.
The plan is to replace it a little further down the line, when the tractor has worked off some of its restoration cost.
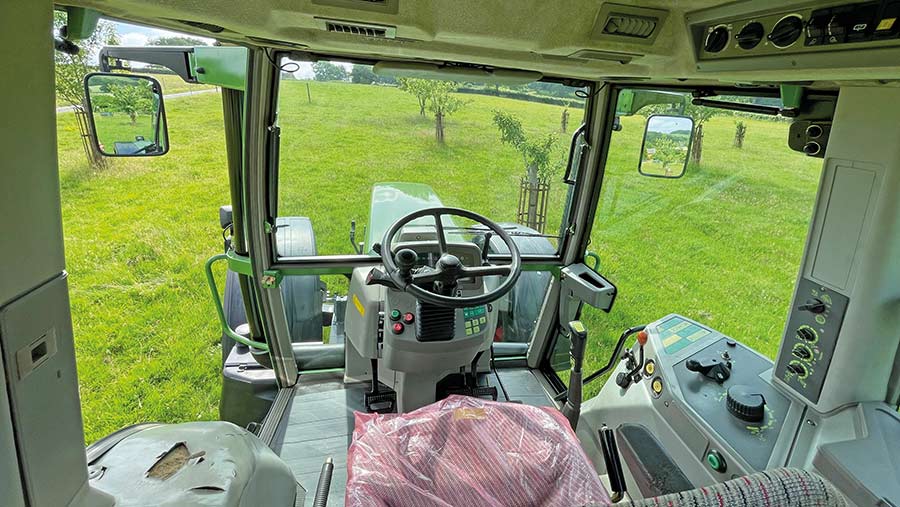
© MAG/James Andrews
Wheels are repainted and shod with quality-but-affordable BKT tyres.
The fronts are 540/65 R28s that had been replaced shortly before the tractor went in for renovation, while the rears are a new set of 580/70 R38s.
It used to have 650s, but the 580s were £500 cheaper and they looked a better size for the tractor.
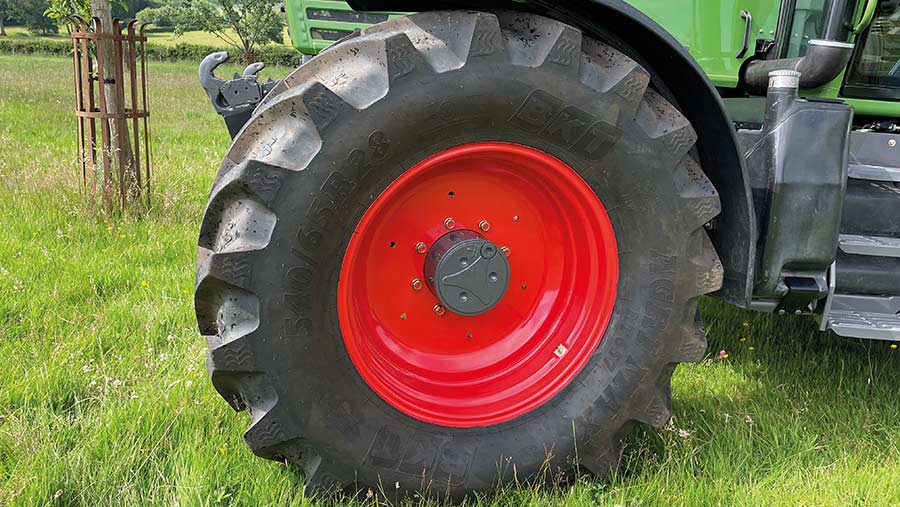
© MAG/James Andrews
The engine is in good order, but it does have the pump turned up to give it a bit more power.
Some of these MWM blocks suffer from leaking O-rings on the piston liners, but they’re dry on this one, so are left as they are.
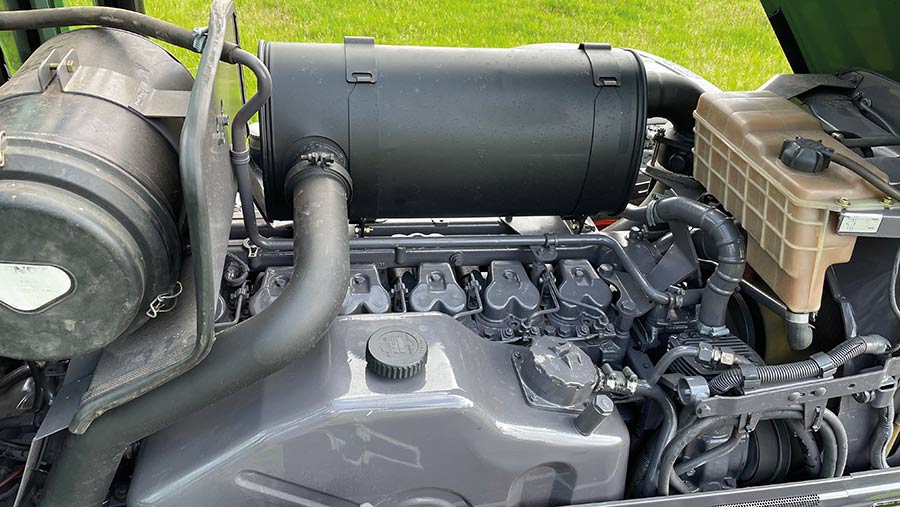
© MAG/James Andrews
After more than 280 hours of work, the tractor is ready to go back to business. The controls are functioning, and the 515 looks almost as good as it did when it left the factory.
As it’s going to be a working machine, rather than a showpiece, any original components that were in decent condition, such as the lightly scuffed front fenders, are reused.
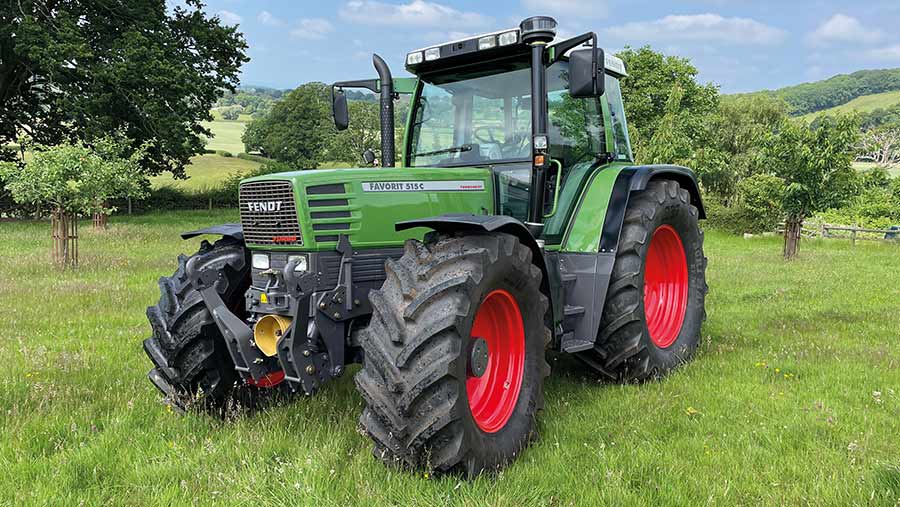
© MAG/James Andrews
Parts and prices
Even though the tractor is more than 20 years old, parts were relatively straightforward to source. Some were surprisingly cheap, others ludicrously expensive, but they averaged out at a reasonable price.
Pigeon House Farm and MRB Engineering
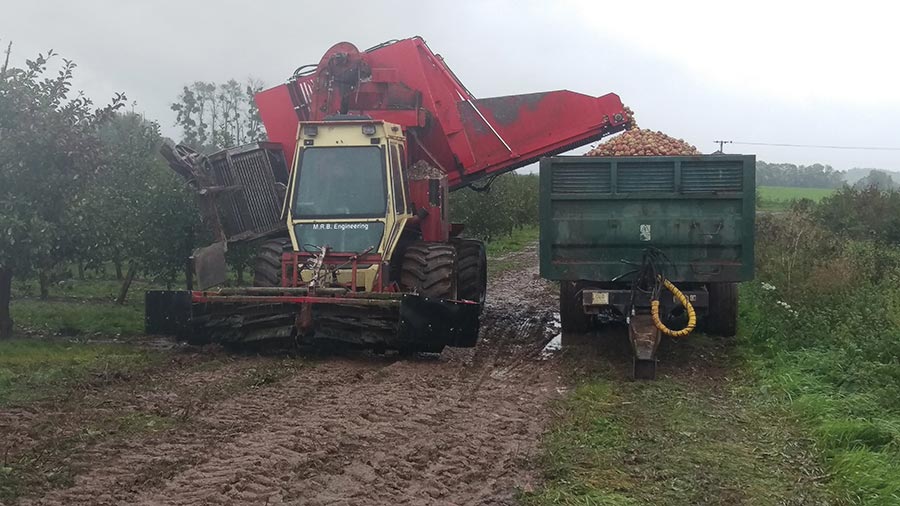
© MAG/James Andrews
Matthew Barnett farms 285ha near the market town of Hereford, with a mix of grassland and cider apples grown under contract for Bulmers and Thatchers.
Some of the pastures support a 90-head suckler herd plus followers, and the rest is used to produce hay and silage to sell on.
In addition to his farming, Mr Barnett runs a groundworks and engineering business with his brother Russell and contract picks cider fruit.
The engineering side specialises in the fabrication of steel frame buildings, but it also designs and builds equipment for planting and harvesting apples.
When Hereford’s cider apple business was booming, this was the main part of the business, and there are several MRB Engineering machines still working in the UK.
These include the tree shakers and self-propelled harvesters that the Barnetts use for their own contracting business – they shake 240ha of trees a year and pick up 120ha of apples.
Shaking machines are tractor mounted, with a hydraulic arm featuring a padded clamp that grips around the trunk of the tree.
An over-centre weight connected to the pto causes the arm to vibrate, dropping the apples to the ground.
One of their three own-built self-propelled harvesters then comes in to collect the fruit. These are based on old low-ground-pressure self-propelled sprayers, built by Everard and Cleanacres.
They work by picking fruit off the ground and sending it up a series of webbed elevators that allow debris to fall through.
Cleaned apples then drop into a hopper mounted where the spray pack would normally be, and another elevator discharges them into a trailer at the end of the row.