How a dairy is harvesting methane to save on diesel costs
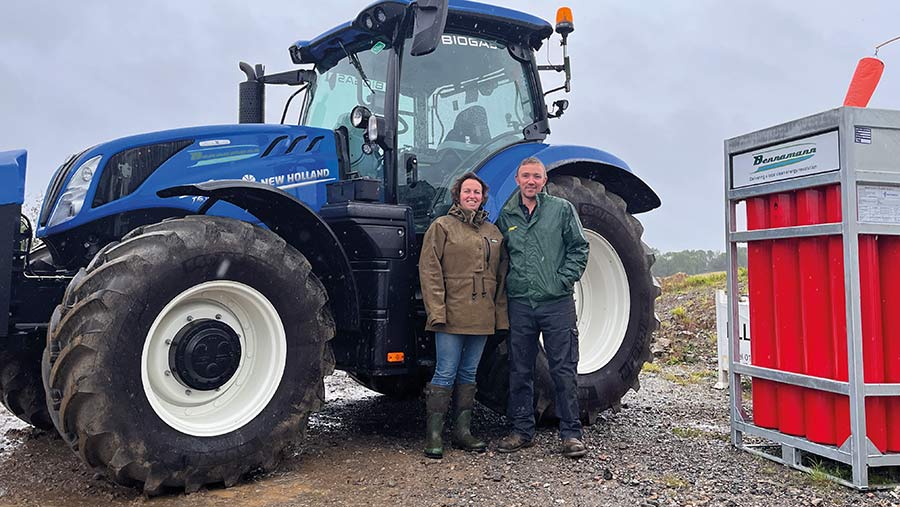
Dairy farmers Kevin and Kate Hoare are mitigating the effects of soaring diesel prices by running a tractor on methane harvested from the slurry pit.
Trenance Farm in Cornwall was in desperate need of new slurry storage when the Hoares took on the tenancy in 2018.
The couple embarked on the development of a covered slurry pit with methane-harvesting facilities in partnership with Cornish renewable energy firm Bennamann and their landlord, Cornwall County Council.
See also: Methane-trapping GreenShed – the climate-friendly future of beef farming?
Farm facts
Trenance Farm, Tideford, Cornwall
- 56ha (134 acres) on 12-year farm business tenancy started in 2018
- Off-lying 23ha (56 acres) rented separately for heifers
- Milks 111 British Friesian cows twice a day, supplying Arla
- Grass-based system, housing when necessary
Methane harvesting started this year and the couple now runs a New Holland T6.180 Methane Power tractor, provided by CNH Industrial, which contains gas cylinders in place of a diesel tank.
They are also trialing a methane-powered generator, which has the potential to slash electricity bills.
As well as capturing enough slurry-sourced fugitive methane to power the tractor, the system produces a liquid digestate that can be applied to grassland via a trailing shoe.
This is not only helping to reduce input costs for the dairy business by saving on diesel and fertiliser, but it is also reducing fossil fuel use, greenhouse gas emissions and decreasing the farm’s carbon footprint.
Capture and use of methane
The sealed, covered slurry lagoon has a holding capacity of nearly 500,000 gallons and complies completely with the government’s Clean Air Strategy rules.
It provides enough storage for slurry from 120 cows for six months.
“The challenge we set ourselves was to efficiently manage an inconvenient waste – such as cow slurry – and, in doing so, turn a powerful greenhouse gas into a clean vehicle fuel, helping to slow down climate change,” says Bennamann co-founder Chris Mann.
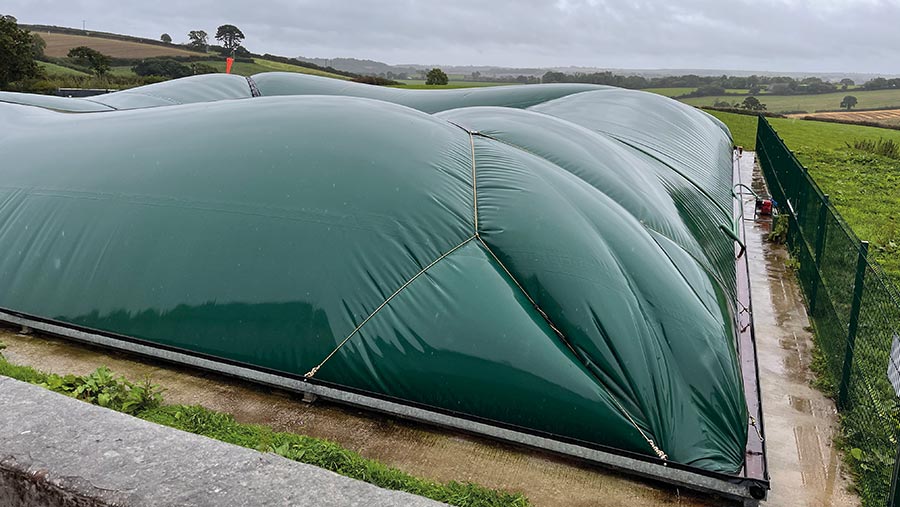
© Hayley Chapman
Late September, when cows were only housed at night, the lagoon was 30% full. At this time, the system would have been able to fill up to a bottle pack a day – the equivalent of 130kg of methane.
The T6.180 tractor will run for about four hours doing typical yard work such as feeding, fuelled by the cylinders under the hood.
However, the latest version has a “range extender” that contains additional cylinder storage in a box where the front weight would usually sit – this doubles its work hours.
The tractor is available to buy and retails at about 20% above the price of the equivalent diesel-powered model.
Financial returns and compromise
The process results in an easy-spreading slurry, Mr Hoare says, because the bacteria in the pit break down the solids.
They are also using slurry analysis so they know what they are spreading and can refine application of nitrogen, phosphate and potash.
When the couple first started farming at Trenance, they bought 25-30t of fertiliser a year.
This has been reduced to 16-18t. With prices hitting dizzying heights this year, the savings are significant.
And they estimate that with a tractor and generator running on methane, diesel use will be down about two-thirds.
Previously, they used 1,000 litres a month, so the reduction brings financial and environmental benefits.
“We have been incredibly lucky – we haven’t had to put our hands in our pockets because Bennamann funded the project with the help of a green energy grant from the council,” says Mr Hoare.
Without this backing, it would have cost about £250,000 for the covered slurry lagoon, including construction, and the pump room, as well as £250,000 for the BioCycle equipment that processes the gas.
However, this equipment is mobile and could be shared by four to five farms to help offset some of this cost.
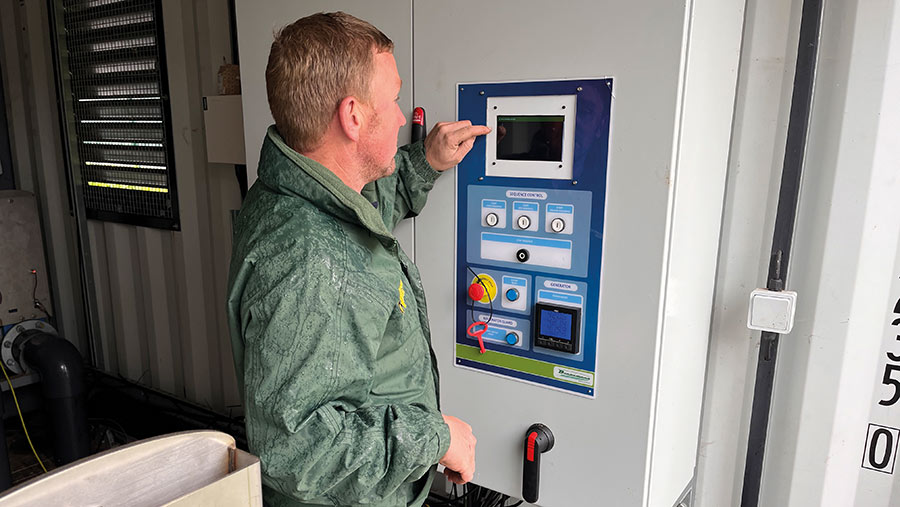
Kevin Hoare can control slurry mixing from the pump room © Hayley Chapman
Dr Mann believes the payback period for installing a system such as this is four to six years if factoring in revenue from gas sales.
Bennamann manages the sale of surplus gas and subsidies, and distributes revenue back to farmers in a profit-share arrangement.
Currently, its primary customer is Cormac, a Cornish council company that runs a fleet of methane-powered road repair vehicles.
Cow management changes
Some elements of Trenance’s cow management had to change to suit the new system. Lignin in the sawdust previously used to top cow mattresses interferes with the slurry bacteria in the lagoon.
Because the Hoares wanted to avoid sediment in the tank from sand, the only option was to use paper bedding.
“It works fine for the cows. There have been no health issues from the change, but it is double the cost of sawdust,” concedes Mrs Hoare.
Paper costs about £220/t, including haulage, compared with sawdust at £90/t. However, the Hoares can reduce this to £155/t if they buy 22t in bulk.
Similarly, formalin can hinder gas production, so it must not be used in foot-baths – instead, they use Pruex products for udders, cow beds and feet.
Sustainable progress
The Hoares want to use methane to power more of the farm in the future.
“Our long-term goal is to get a hybrid generator running on the gas, then switch the electricity off and go off-grid, with the farm, vehicles and house running on the generator,” says Mrs Hoare.
“We should have enough to power the generator and the tractor and then sell the surplus, but how much it’s worth is still unknown,” she adds.
They are looking into new research on boluses that reduce methane emissions via belching.
These could prove especially effective if they result in more methane emitted in manure, because that gas can be harvested.
How the methane harvesting process works
Slurry is scraped into a reception pit and then pumped underground into the middle of the slurry lagoon.
The lagoon has two layers of cover above the slurry to capture waste methane and then store biomethane.
The first cover traps the raw biogas emitted, which still contains hydrogen sulphide – a gas that is hazardous to human health.
This gas goes through a filtration system and is pumped back above the first cover and below the second/top cover.
Gas can remain there – there is capacity for up to one month’s worth – until processed.
At harvesting, the gas goes through another process called the BioCycle, to remove carbon dioxide and compress it to 200bar of pressure before it is pulled off into gas bottles.
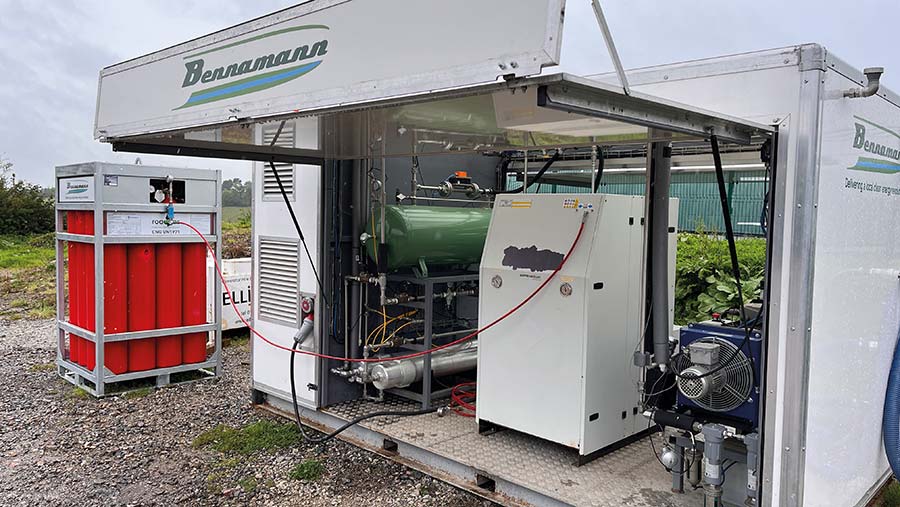
The BioCycle equipment © Hayley Chapman
Slurry needs to be mixed to promote gas production, and this can all be controlled in the pump room next to the lagoon, or through an app on Kevin Hoare’s phone.
The result is a clean fuel, with ammonia and nitrogen oxides also removed, which can be used to power methane engines.
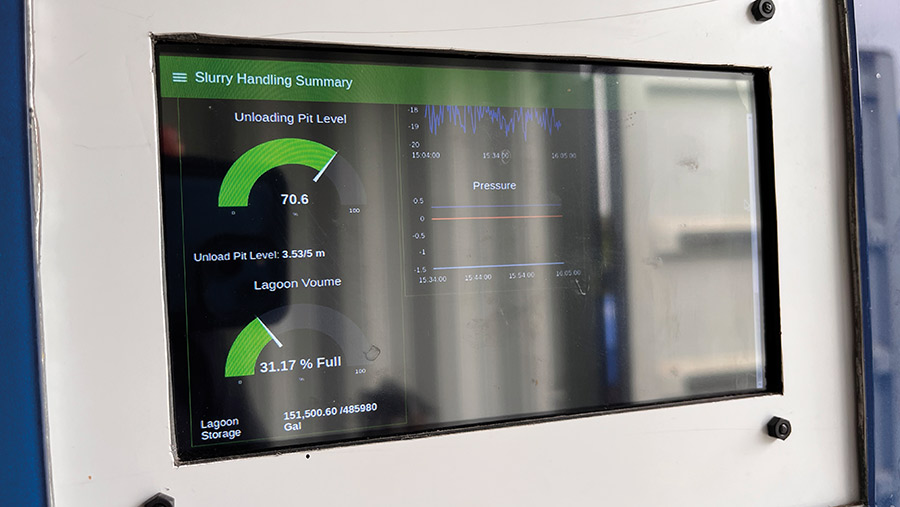
The pump room control panel © Hayley Chapman