New slurry treatment fixes N from air to create enriched fertiliser
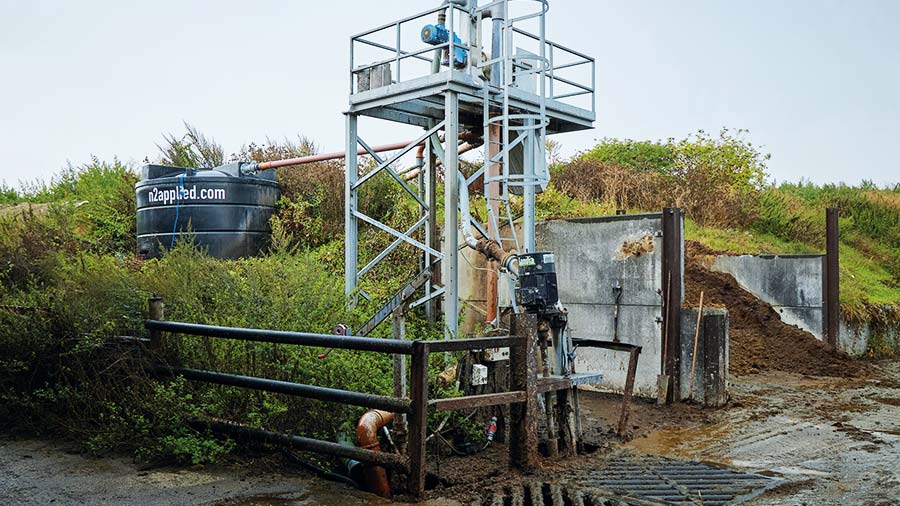
A novel slurry treatment unit that boosts the nitrogen content of liquid manures, using only air and electricity, aims to help farmers reduce reliance on artificial fertiliser, improve crop performance and eliminate methane emissions.
The scalable on-farm technology, developed by Norwegian agritech firm N2 Applied, fixes N from the atmosphere to create a nitrogen-enriched organic fertiliser (NEO).
Through the treatment process, crop-available nitrogen is doubled and nitrogen use efficiency is greatly improved.
Trial results reveal an average yield improvement of 36% and nitrogen uptake improvement of 31% compared with untreated slurry.
See also: How Kent grower plans to farm with no synthetic N fertiliser
Watch the video about the slurry technology and read the rest of the report below.
Matches ammonium fertiliser
The enriched slurry also matches performance levels of a typical ammonium fertiliser.
This reduces the reliance on artificial fertiliser produced using fossil fuels, creating a more secure and localised production facility, right where it is most needed.
Slurry has an average nitrogen content of 1.5kg/t, while treated slurry contains an additional 2kg/t, to total 3.5kg/t.
“This increases the amount of nitrogen delivered to plants, and improves air quality by reducing emissions and removing odours,” says Nick Humphries, the company’s chief agronomist and UK team lead.
At an Adas trial site in Nottinghamshire, the application of NEO to a crop of wheat demonstrated a 43% increase in crop yield when compared with plots using untreated organic fertiliser.
This was alongside a 50% increase in N uptake by the crop, which was contained as protein.
Grass trials carried out by Scotland’s Rural College in Aberdeenshire, demonstrated NEO increased N uptake by 20% compared with untreated slurry across two silage cuts.
Based on crop-available N applied, nitrogen use efficiency averaged 48% for NEO, compared with 31% for untreated slurry and 50% for calcium ammonium nitrate fertiliser.
Emissions reduction
The slurry-zapping process also significantly reduces ammonia emissions, which currently see an average nitrogen loss of 26% if applied from untreated liquid wastes, with a high of 49% N lost.
In comparison, NEO experiences an average nitrogen loss of just 6%.
“This is because the slurry pH becomes acidified, dropping from 7.5-8 to 5-5.5pH. Any unstable N is no longer lost as ammonia gas and instead is retained in the form of nitrate,” says Dr Humphries.
In addition, methane is almost entirely eliminated, leading to significant reductions in the carbon footprint of livestock production.
Indirect advantages of the technology mean slurry storage covers, slurry bugs and injection applications are no longer required, as methane emissions are near to zero.
The machine currently costs £200,000, but skyrocketing fertiliser prices could go a long way to offset investment costs.
How it works
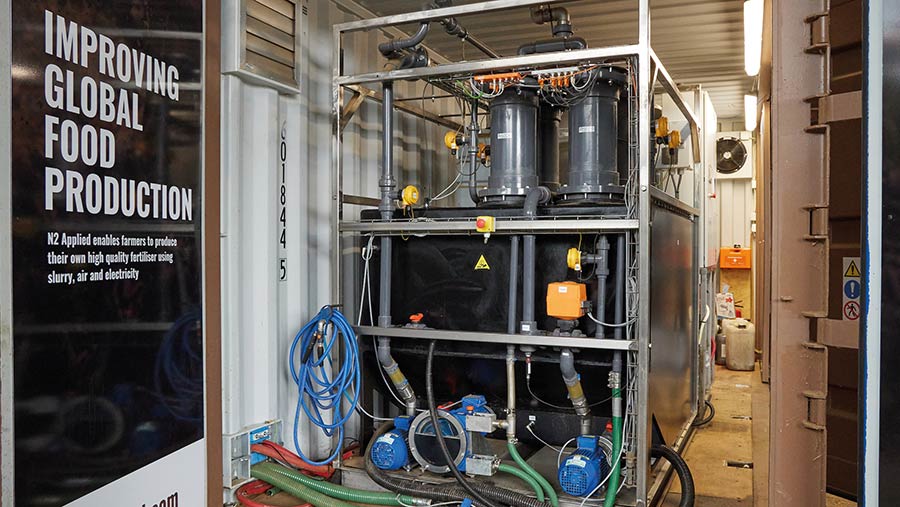
N2 unit © Matt Writtle
Invented in Norway 100 years ago, plasma arc technology was once the main rival to the well-known Haber-Bosch process, which was favoured due to the abundance of cheap gas and oil.
However, with rising oil prices and the government’s push for greener technologies, Agrotech company N2 Applied took the opportunity to build on this existing tech to develop their slurry-zapping, nitrogen-enriching plasma machine.
The unit, which fits into a converted shipping container situated on farm, works in a two-part process, explains N2 Applied’s Nick Humphries.
“The plasma arc compresses air and uses electricity to fix nitrogen to create a reactive nitrogen gas [NO]. The gas is then pumped through the absorption system, where it comes into contact with the slurry.
“This increases the nitrogen content of the slurry, making it a better fertiliser,” says Dr Humphries.
This process is fundamentally the same as when nitrogen is fixed during lightning storms, which has the ability to fix an additional 20kg N/ha/year.
“The machine features a 50kW system which is quite energy intensive, but this can be scaled up or down to as low as 12kW. If there are renewable energy sources on farm this helps to offset energy costs.”
Kitted out with two circulation pumps, a discharging pump and an in-feed pump, slurry is slowly drawn into the absorption system, where 1.6cu cm of slurry is present in the tank at any one moment.
Operating 24 hours a day, the machine runs in continuous batches, treating enough slurry for a 200-cow unit, at a target of 8,000 hours/year.
“Treatment capacity is affected by the nitrogen concentration, regardless of the water content,” says Dr Humphries.
Product specialist and engineer Gareth Coates says remote monitoring is possible thanks to a number of sensors that constantly monitors the machine, recording 2,000 data points each second.
“The team have two dedicated remote monitors based in Norway, and a number of engineers across the UK. This allows any issues to be resolved before the farmer is even aware.”
However, he says the treatment plants cannot treat anything with a particle size greater than 3mm, but there is scope to increase this as the technology develops.
Slurry-treatment project at Buckinghamshire dairy farm
A group of MPs on the Environment, Food and Rural Affairs (Efra) committee visited one of the six pilot slurry treatment units across the UK in early September, as part of the food security inquiry.
The visit took place at Buckinghamshire dairy farmer Neil Dyson’s Holly Green Farm, home to the Arla Innovation Centre.
This was the very first farm in the UK to set up the technology 18 months ago as part of the company’s pilot launch.
Mr Dyson said: “We have experienced how this technology can fit into our existing farm environment, and explored its potential for suppressing emissions and producing natural fertiliser on site.
“It is a breakthrough that holds great potential for UK food production if pioneering farmers can be helped to introduce it, and so convince others to follow their lead.”
The Efra food security inquiry aims to identify factors currently affecting food supply chains and food prices such as the war between Russia and Ukraine, both of which are major exporters of fertiliser.
The MPs discussed what role government can play to encourage initiatives that help make the UK more self-sufficient in food production.
The MPs who took part were:
- Sir Robert Goodwill MP (chairman of the Efra committee and Conservative MP for Scarborough and Whitby)
- Ian Byrne MP (Labour, Liverpool, West Derby)
- Barry Gardiner MP (Labour, Brent North)
- Julian Sturdy MP (Conservative, York Outer)
- Rosie Duffield MP (Labour, Canterbury).
Sir Robert said: “Given the pressures facing UK farmers and food producers, we need to look at innovative solutions to help strengthen our food security.
“Fertiliser prices are currently high. This technology – which creates a richer fertiliser while reducing the pollution associated with slurry – sounds like a step forward. It could help both farmers and the environment.”