Farmers Weekly Awards 2023: Pig Farmer of the Year finalists
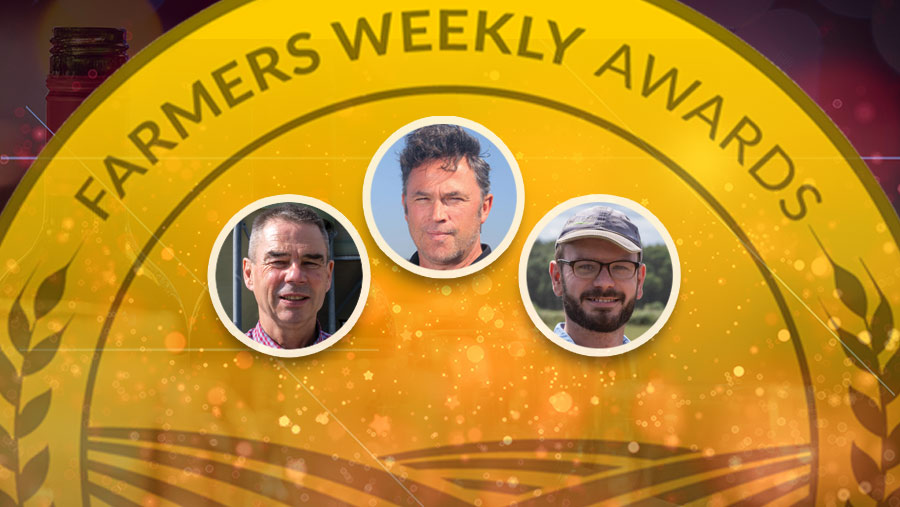
An outdoor breeding setup, a tented nursery and an indoor breeder-finisher were competing for top spot this year.
While their units varied widely, the three finalists shared a determination to succeed based on business acumen and attention to detail.
See also: See the full 2023 Farmers Weekly Awards shortlist
The finalists
William de Feyter
Green Farm Livestock, East Ruston, Norfolk
Guy King
GSK Pigs, Dereham, Norfolk
Frank Tobin
Brandy Wharf Piggery, South Kelsey, Lincolnshire
The judges
The judging team visited each finalist for a three-hour interview and a tour of their systems.
David Fulton
Last year’s winner
Judith Tooth
Farmers Weekly livestock editor
Charlie Dewhirst
Senior policy adviser, National Pig Association
William de Feyter
Green Farm Livestock, East Ruston, Norfolk
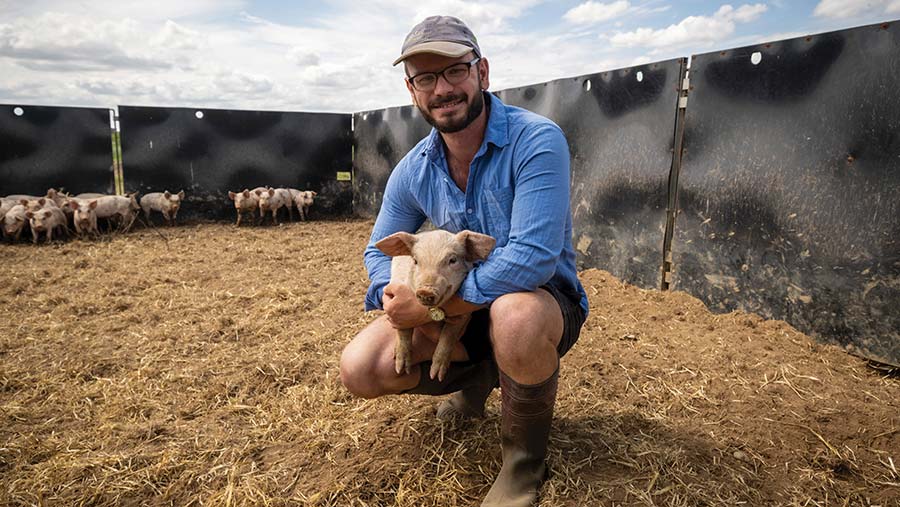
William de Feyter © Jason Bye
Farm facts
- 4,810 pigs on three straw-based units
- 4,200 reared in tents, and 450 indoors, from five weeks to 40kg
- 160 small pigs finished indoors
- Red Tractor and RSPCA assured
- 32ha grass on grazing licences
- 100 ewes producing lamb sold direct
William de Feyter, who farms with his wife and business partner, Sarah, studied farm business management at Harper Adams University and set up in pigs in 2014.
He cut his teeth on an 850-place, wean-to-finish indoor unit, but had to give it up when the farmyard was developed for tourism.
Losing that unit kick-started a new venture using 35 second-hand tents on 4ha (10 acres) of grass rented from his parents.
He signed a five-year contract-rearing agreement with BQP, which enabled him to attract start-up capital. He is on course to hit a budgeted three-year payback.
William also took on a set of buildings to finish 160 small pigs from the tents, and runs a 450-place indoor nursery unit.
System
He provides accommodation, straw and labour, while BQP supplies the pigs, feed and veterinary and technical support.
He receives a monthly flat rate for each pig place, plus bonuses for good feed conversion ratios (FCR) and low mortality.
When weaners arrive, they have already been introduced to a creep starter.
He continues feeding this for a week before moving them onto weaner pellets. For the final week before they move on to BQP’s finishing units, pigs switch to grower pellets.
The tents accommodate 4,200 pigs from five weeks old to store weight. Made by John Harvey Engineering, the tents were 10 years old when William bought them.
He reckons they could last another 15 years. “You can easily replace a canvas or a bent pole, and it’s not silly money,” he says.
Tents are dragged onto new ground after each batch of pigs. After three years, the site rotates to a fresh field.
Straw-for-muck arrangements are in place with three farms, all within five miles. Each batch produces 600-700t of muck and uses 300-350 round bales plus 70-90 square ones.
Health and welfare
Bedding and feeding are done twice weekly by William or his part-time, self-employed pigman, John Bell.
All pigs are checked twice a day. BQP vets draw up a herd health plan and visit quarterly – or more frequently if a health issue arises.
The tents are served by two water lines, each fitted with a Select Doser system, so medication can be directed at specific tents, rather than giving blanket treatment.
This allows for more responsible use of antibiotics, says William. When not medicating, the water is run with a broad-spectrum biocide to ensure it is free of biofilm and bacteria.
William gets daily water consumption updates via his mobile phone. Any significant change in intake alerts him to consult his vet before a health issue arises.
He has moved entirely to intradermal vaccination. “There are no bent needles and it’s clean, easy and quick,” he says.
Wider view
William is a director of the Aylsham Agricultural Show Association and an assistant head steward at the Royal Norfolk Show.
“It’s a great way of giving something back to the local community and keeps me on my toes dealing with businesses outside the farm environment,” he says.
He is also happy to show anyone around the unit. “I have nothing to hide,” he adds.
Tents have proved to be a low-cost way of expanding and William’s aim is to extend the current site and, in the long term, set up a second site.
He would also like to do a Nuffield scholarship to increase his knowledge of the straw-based pig industry.
What the judges say
Green Farm Livestock is a young business led with enthusiasm, entrepreneurial flair and determination to succeed, along with a willingness to take advice and adopt technologies to help protect pig health.
William de Feyter summary
The judges liked
- Showed entrepreneurial flair by sourcing second-hand tents
- Positive attitude in the face of setbacks
- Use of technology to monitor and improve pig health
- Willingness to take advice
- Good business head
- Involvement in local agricultural shows
The numbers
- 1.82:1 Average feed conversion ratio of pigs reared in tents
- 611g Average daily liveweight gain of pigs reared in tents
- 120 Number of pigs in each tent
- 4.51% Average mortality in tents
- 500m Length of underground water pipe laid for tents
Guy King
GSK Pigs, Dereham, Norfolk
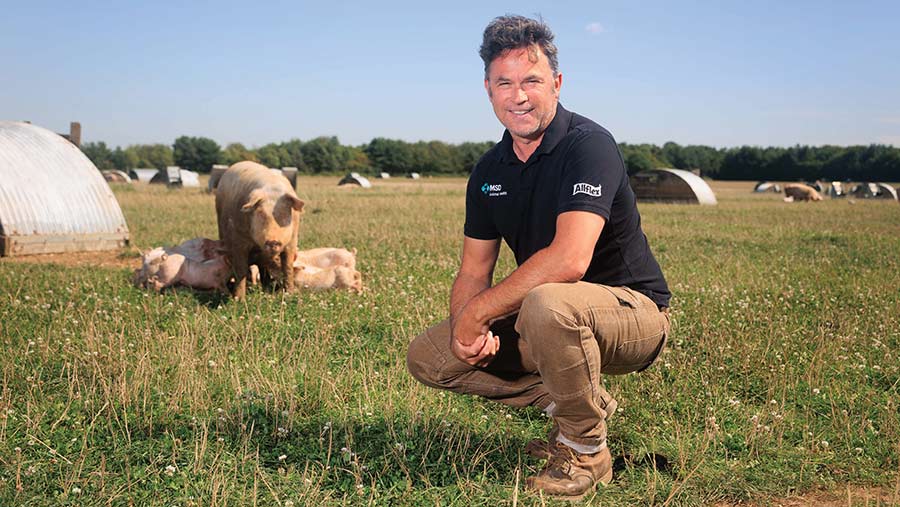
Guy King © Tim Scrivener
Farm facts
- 8,600 sows across nine outdoor units
- All units run on rented land, totalling 445ha
- Two sites are breeder-finisher units
- Red Tractor and RSPCA assured
Guy King’s love for pigs began when he took a Saturday job on a farm with 100 sows. Prior to that, he had no farming knowledge or experience.
He studied at the local agricultural college and worked on various units before branching out into engineering and building. By the time he returned to the pig industry, he had learned that “time is money”.
He set up GSK Pigs in 2005 and now has nine outdoor breeding units run as part of arable rotations on rented land across Norfolk and Suffolk.
System
Every unit is a closed herd and operates independently with its own staff and machinery.
Each has a dedicated area for gilts selected as replacements to grow on, a service radial with a central tent for artificial insemination, dry sow radials, individual farrowing paddocks, and a vaccination pod.
For seven of the units, pig farming operation BQP supplies pigs, feed and veterinary support, while GSK Pigs provides the land, staff, machinery and equipment.
These units have been repopulated with high-health-status stock during the past 18 months.
At the same time, the herds have been switched over to five-week weaning, two-week batching operations. Pigs from these units move to BQP grower units.
In addition, Greenlane Organics is a 400-sow farrow-to-finish setup at Sandringham, run on behalf of the Organic Pig Company, while Bruntona Rare Breeds is the newest venture.
This 200-sow unit also takes pigs to finishing weight; it supplies high-end restaurants and hotels.
Guy is committed to establishing and maintaining green cover on all sites to protect water quality and soil structure.
He has found using a mix of timothy, cocksfoot, fescues and clover produces a resilient and tufty sward that has deep roots.
“It’s a nicer environment for the staff now too, and wear and tear on machinery is less of an issue,” he says.
Health and welfare
Guy prefers to take on staff with no previous pig experience and train them. “Without good staff, I wouldn’t be sane – or where I am today,” he says.
“All pigs are checked daily, and each unit has a dedicated team who know the farm, the pigs, the equipment and the best way to get a job done.”
He has appointed one of his staff, Jason Hindle, as fieldsman to help with the day-to-day running of the units. Part of his role is to make full use of the PigVision management software recently introduced.
This system is linked to ear tags fitted to each sow and will enable data to be called up instantly to inform decisions about performance, feed use and piglet health.
Each unit has a dedicated vet who completes a quarterly health plan with actions that form a working document for the staff.
Wider view
Guy’s aim is to continue growing the business and embracing new ideas and techniques, always with the environment in mind.
Pig shades are being trialled this year and will be rolled out across the units in 2024.
And a tented finishing system is being introduced at Greenlane Organics with the aim of improving daily liveweight gain and reducing days to slaughter.
Guy is also developing an in-house staff training facility with guidance from Andrew Palmer, AHDB knowledge exchange relationship manager for the pork sector.
“If you keep doing what’s best for the pig, then the pig does right for you,” he says.
What the judges say
GSK Pigs comprises nine outdoor breeding units with a strong focus on high welfare and environmental standards and close monitoring to ensure healthy pigs perform consistently across the board.
Guy King summary
The judges liked
- Growth and development of business from scratch
- Clear staffing structure and opportunities for progression
- Commitment to maintaining green cover on all sites
- Good working relationships with landlords
- Good understanding of the value of outdoor pigs in an arable rotation
- Investment in technology to improve pig health and welfare
The numbers
- 59 Total number of staff
- £9 Cost/kg for grass seed mix, sown at 9-10kg/ha
- 25.03 Average number of pigs weaned a sow a year*
- 8.52kg Average weight at five-week weaning*
- 12.2% Average pre-weaning mortality*
*Figures based on gilt herds
Frank Tobin
Brandy Wharf Piggery, South Kelsey, Lincolnshire
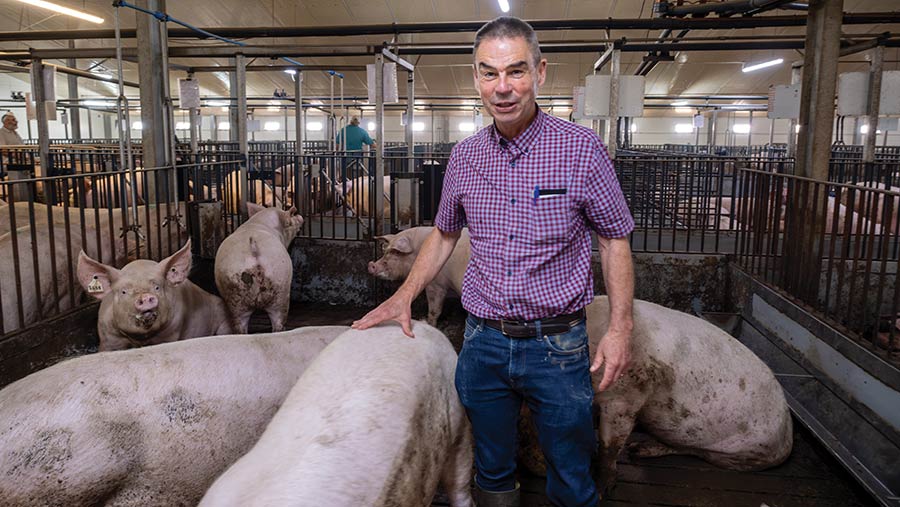
Frank Tobin © Jason Bye
Farm facts
- 500 F1 sows bred from Danish Landrace nucleus herd on separate unit
- All progeny reared to bacon weight
- On-site feed mill
- Computerised wet feed system
- Supplies finished pigs to Karro Food Group
- Red Tractor assured
Dogged determination to succeed as a pig farmer has got Frank Tobin where he is today, with a 500-sow, indoor breeder-finisher unit on a purpose-built site in north Lincolnshire.
Initially, Frank – who also leads a York-based veterinary practice specialising in pigs – was a shareholder in an outdoor pig organisation.
When that got into difficulty, he bought the indoor pigs from that outfit and set up on his own. He then took on a finishing unit, but the buildings were of poor quality and the venture was “a disaster”.
Undeterred, he bought 1.2ha of arable land at Brandy Wharf, where he built two finishing sheds and a feed mill in 2011. Four years later, he added farrowing and dry sow accommodation, and moved his pigs there.
System
The unit at Brandy Wharf was built for 600 sows weaning 12 pigs a litter.
However, since introducing Danish genetic stock four years ago (chosen for prolificacy and growth rates) and using a careful process of staged fostering, final litter size has risen to 15 pigs.
To accommodate the increased productivity, herd size has been dropped to 500 sows. “The advantage for us is fewer sows, and we’re still weaning a decent pig,” says Frank.
The whole unit is slatted and slurry-based. This suits the wet-feeding system Frank chose, making use of a wide range of crop co-products including liquid potato, whey, yeast and distillers’ grain.
“When I set up the unit, there was a saving on each of these liquids,” he says. “It isn’t what it was, and energy costs are higher, but there is definitely still a saving.”
The biggest economy, however, comes from milling all feed on site. Wheat and barley are bought from, and stored at, local farms.
Soya is also used, but by including co-products such as yeast, less is needed, saving cost and lowering the unit’s carbon footprint.
Feed is made fresh each day. Rather than pre-mixing all the dry ingredients, they are kept separate so any adjustments to rations can be implemented quickly.
After weaning, pigs are fed two creep diets – also milled on farm – before moving onto a weaner diet.
All finished pigs have left the unit 20 weeks after weaning, at 95kg deadweight, with the biggest pigs pulled out three to four weeks early.
Health and welfare
High standards of biosecurity are maintained to minimise disease risk.
Although Frank is himself a specialist pig vet, he recognises the value of an outside eye and takes regular advice on pig health, welfare and nutrition.
Heated mats keep piglets warm in the farrowing rooms, while a misting system cools sows, second-stage weaners and finishers on hot summer days.
Frank’s confidence in his team of four staff is clear: he spends just one a day a week at the unit.
“We’ve got a stable staff structure, and they’re a good bunch of lads,” he says, adding that they have PigVision software to aid herd management.
Wider view
Frank collaborates with a neighbouring farmer, whose land surrounds the pig unit, to manage slurry, which is pumped underground and accessed via hydrants for spreading using an umbilical system.
He also sits on Sainsbury’s pig production group, which has a particular focus on finding ways to improve sustainability and lower the carbon footprint of pig production.
Attempts to get planning permission to extend the site at Brandy Wharf have so far failed, but Frank did set up another 600-sow pig unit north of York last year.
What the judges say
Brandy Wharf has been built with pigs and staff in mind and is managed efficiently as a result. Productivity is high, while milling feed on site and using liquid by-products keep costs down.
Frank Tobin summary
The judges liked
- Innovative, flexible feeding system
- Use of by-products to reduce feed cost and carbon footprint
- Well laid-out unit for effective workflow and biosecurity
- Strong team keeping a clean and tidy unit
- Close attention to detail
The numbers
- 22 Farrowings a week
- 15.4 Average pigs weaned a litter
- 34.58 Average number of pigs weaned a sow a year
- 1.94 Carbon footprint for nursery unit (kg carbon dioxide equivalent/kg liveweight)
- 25 Percentage of energy demand supplied by solar panels on farm
The FW 2023 Pig Farmer of the Year is sponsored by Pilgrim’s UK
“As the UK’s number one higher-welfare pig farmer, we are delighted to sponsor the Pig Farmer of the Year award, recognising the innovative, hard-working individuals working in our sector.”
Fábio Brancher, operations director, agriculture, Pilgrim’s UK