Robot dairy saves £30k with custom microgrid system
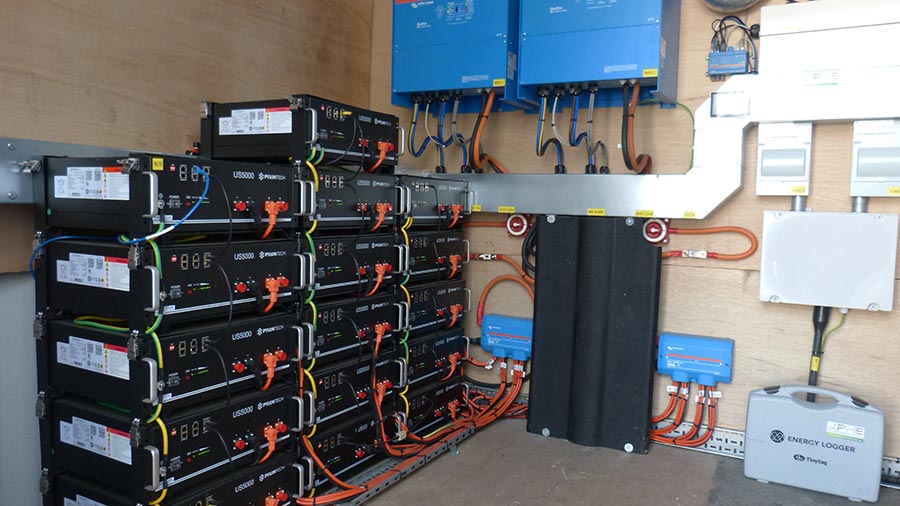
A robotic dairy farm, currently producing 97% of its power needs through solar panels, is entering the third stage of energy profiling to optimise its own self-contained energy system or custom microgrid.
Billy and Marion Muir of Broompark Farm, Glenluce, installed 80kW of solar panels and 75kW of industrial battery storage in a custom microgrid (CMG) – made up of solar panels and industrial battery storage – this spring, after electricity prices rose from 15p/kW to 66p/kW.
See also: Farmer Focus: Fog lifts on new solar panels and cosy cabin
Faced with a potential bill of more than £55,000 a year, the Muirs initially thought they would only save £15,000, because Scottish Power’s local grid constraints would limit them to producing just 50kW from the panels.
Such constraints are in place across several regions of the UK.
However, because the Muirs installed a CMG, it bypassed grid constraints and allowed them to increase energy production to an initial 80kW.
Doing this has saved them £30,000 on their bill in five months.
The saving comes from offsetting high import tariffs, rather than selling their surplus power back to the grid for up to 15p/kW.
Project costs are written off at 12p/kW for the next 25 years, a saving of 54p/kW at current prices.
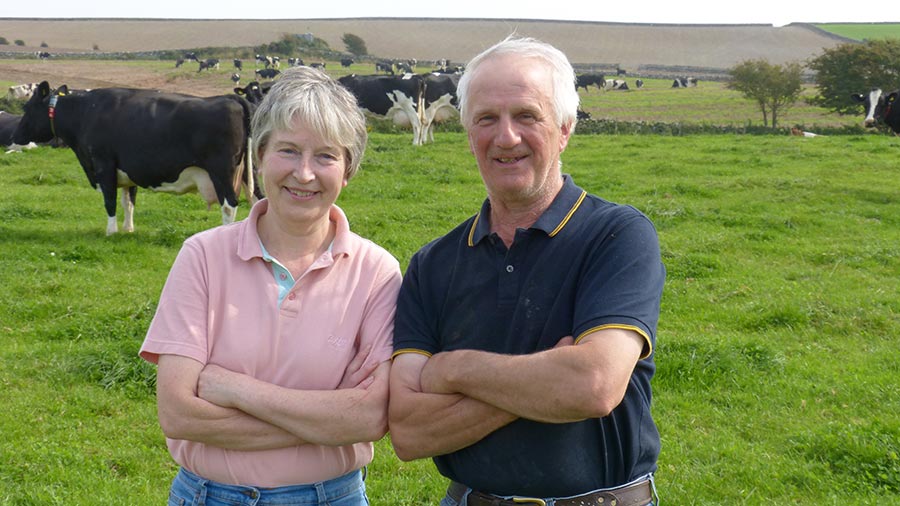
Marion and Billy Muir © MAG/Michael Priestley
Farm facts: Broompark Farm
- 140 cows milked on three Lely robots
- British Friesian-based herd
- Grazing system allowing cows access to robot shed
- 125ha, of which 20ha growing barley and wheat
- Cereal harvested at 18% moisture and urea treated
- All-year-round calving
- Protein bonus supplying Lactalis, Caledonian Cheese
- Average yield 9,000 litres at 4.37% butterfat and 3.22% protein
Custom microgrid
A renewables expert advised the Muirs to install a CMG, which, uniquely, allows direct current (DC) power from solar panels (also wind turbines and other renewables) to be fed directly to battery storage.
This stored energy is converted to alternating current (AC) power for use by the farm, on demand.
This “zero-export” system does not supply power to the grid, it only pulls power from it when the batteries run low on stored energy.
“We are better off doing it this way,” says Billy. “We’d been toying with the idea of getting solar panels for several years and the electricity cost gave us the kick we needed.”
The CMG system is bespoke and allows both flexibility and expansion after initial installation. Farmers Weekly asked about the process.
Stage one: Energy profile
The Muirs called on the services of Dumfries-based specialist microgrid installer Paul Hamid, of PH Energy Systems, who recommended they get independent advice on setting up a CMG and creating an energy profile for the farm.
They were referred to renewables consultant Dougie Blair, of Beyond Innovation, who oversaw the system’s design.
Initially, he generated an energy profile, analysing 12 months of electricity usage.
He backed this up with a 24-hour, second-by-second monitoring of the farm’s demand using an energy monitor.
Dougie advised the Muirs to install a CMG, comprising 80kW of solar panels and 75kW of battery storage.
This was conservatively estimated at providing 65% of the farm’s annual power requirements.
Stage two: Installation and summer use
An initial monitoring period started on 20 April this year.
This involved close analysis by Beyond Innovation of the production, demand and storage of electricity by the CMG’s unique product support and app.
The following key decisions and observations were made:
- Installation 196 solar panels were DC-coupled to the CMG.
- Power The panels were installed on the robot shed’s fibre cement roof.
- Microgrid The microgrid was housed in an airtight shipping container with an air extraction system to keep dust to a minimum. Fifteen 5kW lithium batteries were installed within the CMG to store energy for powering the farm and robots. AC inverters convert DC stored power in the batteries for use on the farm when energy is needed, to minimise power conversion losses.
- Grid usage The farm’s demand fluctuates around 6kW all day, with peaks of 18kW, and troughs of 3kW at 5am. A top-up of power from the grid was noted at 6am-7am each morning. (The CMG imports power if insufficient stored energy is available to meet the farm’s requirements).
- Functionality Even on a dull and rainy day the batteries achieved 100% charge status by late afternoon.
- Financing The Muirs opted to pay for the system with cash from an individual savings account. They were offered 8% interest rates at the time. Investments in renewable energy attract 100% first-year tax allowance, with unused allowances being carried back or forward.
- Monitoring Beyond Innovation monitored the usage, demand and battery capacity daily, identifying an increase in consumption at weekends when staff routines changed and machines were left switched on for longer.
The process took three weeks from making the initial inquiry, to conducting an energy profile, to having the system powering the house and farm.
Stage three: Tweaks for winter
Adjustments will be made to increase battery and solar capacity to manage winter daylight hours after six months of monitoring.
Other options like a combined heat and power system, or freezing and heating water in the middle of the day, will also be evaluated.
The aim is to eradicate any need to use the grid, instead powering up a generator if required.
“I’m keen to stop being a customer of the utilities company entirely,” explains Marion.
“The standing charges are £550 a quarter. That’s over £2,500 a year to buy next to no electricity.”
The Muirs expect to have the system optimised for their needs by the spring of 2024
Excessive grid connection waiting times should improve
Lengthy grid connection waiting times for renewables projects – sometimes stretching into the 2030s – are set to be addressed by legislatory reform, says solar industry trade body Solar Energy UK.
But until then, establishing a microgrid can get around such problems and constraints, it says.
“Fortunately, reforms are under way that will bring waiting times down considerably,” said a spokesman.
“The way that connection queues are managed by distribution network operators is being streamlined, Ofgem will allow them to loosen the purse strings for investment in grid reinforcement, and Whitehall has also recognised the issue as a significant stumbling block on the way to net zero.”
But Beyond Innovation’s Dougie Blair says that with large roof spaces and big energy requirements, UK dairy farms have been important customers for solar panel companies wanting quick sales of off-the-shelf 50kW systems to fit within the constraints of district network operators (DNO).
The problem facing some farms is that the solar project they buy is not large enough to sufficiently mitigate a farm’s energy bills because of local DNO constraints, he says.
This is because most of a dairy’s power is consumed when solar production is at its lowest (during early morning or early evening milking).
Dougie advises the following:
- A dairy cow typically consumes 1-2kWh a day
- The cost of a custom microgrid with solar panel system for a dairy farm is typically £100,000-£500,000 with a six-to-seven-year payback
- Retrofitting and expanding existing solar or wind turbine systems with a custom microgrid, irrespective of DNO restrictions, is now possible.