Ultimate guide to tractor tyre management
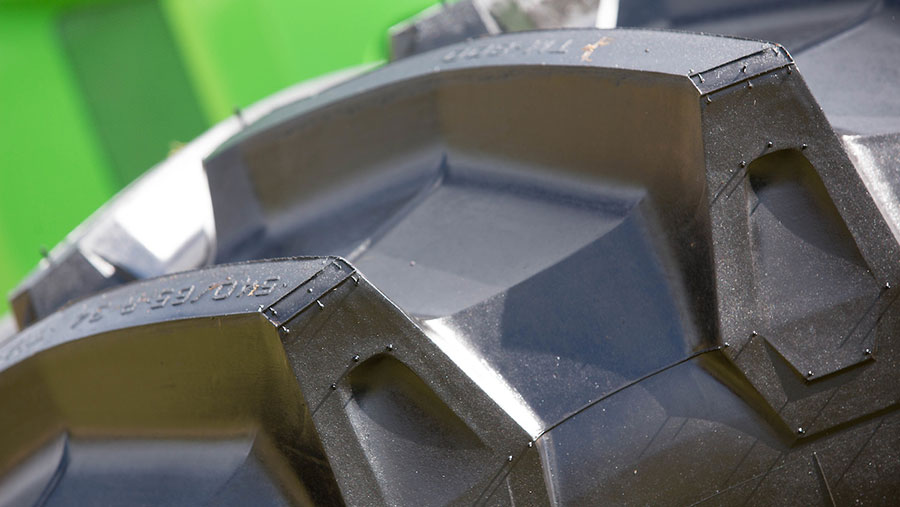
It is essential to ensure your tractor tyres are in good working order, both for your safety and for your pocket.
We look at the causes of premature tyre wear, how to avoid tyre damage and soil compaction and how to check whether your tyres need to be replaced.
More on tyres
See also: Winter tyres: the pros and cons
See also: Tractor tyres: make sure your pressures are right
See also: Tyres v tracks: which is best?
Extending tyre life
Premature tyre wear can be caused by many things, but the most common causes are running them at the wrong pressures, operating in poor conditions and having incorrect wheel alignment.
With a set of front tyres costing from £500-3,000 or more, acting quickly can save money and time.
Alignment
Incorrect wheel alignment is a common cause of irregular tyre wear. This can be costly, not just in replacing the tyres but also in fuel efficiency, particularly when on the road.
Roads are least forgiving when the rubber is pushed sideways on wheels that aren’t parallel. You will first notice this from the wear pattern on the edges of the front tyres.
If the symptoms are spotted early enough, the tyres cna be switched from side-to-side, which will help with the tyre life. But to stop it happening again, you’ll need to adjust the tracking – a job that’s fairly simple to check and adjust yourself.
It may be useful to refer to the operator’s manual for your tractor first, though. If you’ve mislaid it, your local dealer may be able to help you.
The advice here is general, but it applies to the majority of current tractors. You will need something to measure the distance between the wheels; a telescopic pole is best, but a tape measure will suffice if you get someone to help you.
Wheel alignment is best carried out after checking (and resetting if necessary) the track width.
In an ideal world, the wheels should be parallel, but as adjustments can usually only be made in increments of several millimetres, a slight toe-out is preferable to a slight toe-in because of the toe-in pressure under load, such as braking.
- Measure the distance between the wheel rims at hub height at the front and rear of the wheels. Compare the two; if the distance is greater at the front, you have toe-out; if at the rear, toe-in.
- If adjustment is necessary, loosen the locking nut on the track control rod.
- Remove and discard the self-locking nut, usually located on the end of the track control rod. You may need to apply downward pressure on the top of the screw as there is a ball-bearing in the assembly that may cause the nut to spin.
- Extract the track rod end (again, some force may be needed).
- Screw the track rod end into or out of the track rod to shorten or lengthen the assembly as necessary.
- Reposition the wheel as appropriate and reinsert the track rod end; when the wheels are parallel secure with a new self-locking nut. Do not be tempted to re-use the old one as they have a nylon inner which will have been ‘moulded’ to the previous position.
- Finally, retighten the lock nut on the track control rod. This job could save you hundreds of pounds.
Correct tyre pressure
It’s not uncommon for operators to run tyres at too high a pressure and this can cause a number of problems.
High pressure
Tyres become hard and ridged when they are pumped up to a higher pressure than recommend and this makes for a pretty uncomfortable ride.
Grip is also reduced, mainly because there is a smaller surface area in contact with the ground and fewer lugs, thus giving less traction. Spinning wheels damage soil structure and increase fuel consumption, too.
Tyre wear can increase giving a shorter life to the tyre.
Tyres also become more sensitive to impact when they have a high inflation pressure.
Low pressure
Running at very low pressures also has its problems. Increase in fuel consumption, as power is lost through flexing and having too much of the tyre in contact with the ground.
This flexing and bouncing has the added problem of stressing the sidewalls and causing serious damage to the casing. It also causes heat to build up in the rubber, which makes the tyre wear quicker when doing road work.
Stability is reduced too, particularly at higher speeds on the roads.
There’s a higher risk of the tyre turning on the rim during heavy draft work.
Weights and loads
When any equipment is mounted on the rear of the tractor it increases the weight on the rear axle and removes weight from the front axle.
The balance of this weight between the two axles is known as the load distribution.
And it’s important that tyre pressures are adjusted to take this load distribution into consideration. Incorrect loading and tyre pressures can result in too much stress in the tyres, causing them to wear faster, get damaged or cause injury from tyre failure.
Most tyre manufacturers publish tables to help you do this. Many have more sophisticated tools where you can look up the correct inflation pressure and some have digital and app-based tools, too.
If you want to manually work out the extra load an implement puts on an axle you can use the following calculation:
Additional weight = implement weight × distance ÷ wheelbase (see diagram below)
This is a basic calculation, but can also be used for harvesters and trailers.
You’ll still need to look up the recommended pressure from manufacturer’s figures though.
The best load calculators in the market are designed to calculate load per axle according to a tractor’s configuration.
Some can also recommend the optimum pressure for the selected application or ground conditions.
It’s worth taking a bit of time to have a play with these tools as they’ll save you money in the long run and help you do a better job.
Soil compaction
The biggest preventable cause of soil compaction is incorrect tyre pressure. The tyre pressure in your tyre is approximately the same as the pressure you exert on the soil.
You want to aim for as low a pressure as possible in the field. This must not be achieved at the expense of the tyre turning on the rim though.
With the pressure on the soil’s surface the same as the tyre inflation pressure, using a wider tyre at a lower pressure will help reduce the compaction, increase traction and save fuel.
Road transport
It is very important to have the correct tyre pressure when travelling on the road.
Under inflation can be very dangerous causing the tractor to be unstable when cornering. The increase in heat build up also leads to rapid wear.
Equally, over inflation can cause the tractor to be unstable due to the lack of tread area in contact with the road. It also leads to irregular tread wear.
In an ideal world, tyres pressures would be adjusted to suit the job in hand, but realistically this isn’t going to happen. A good compromise is to adjust the pressure to suit the job the tractor will be doing most. But if you are switching form heavy draft work to a large amount of road haulage, it is wise to add some more air.
Central tyre inflation systems are expensive, but they do allow you to run tractors with the optimum tyre pressure at all times.
Tyre technology
Tyre technology is also helping to get round some of these problems. Increased Flexibility (IF) tyres so that the load you can carry at speed at a low pressure is dramatically increased.
This is down to a new sidewall design that means you can set your tyre pressures low for fieldwork safe in the knowledge that they will still perform at high speeds.
If in doubt, seek advice
It is important that tyres be maintained in a good condition at all times and when the time comes to change them, the correct replacements are fitted.
The tyres fitted to your vehicle when new were selected by both the vehicle and tyre manufacturer taking in to account all aspects of work, the size and the horsepower of the vehicle is likely to undertake.
Changes to the tyre size, structure, load and speed ratings should not be made without first seeking advice from the vehicle or tyre manufacturer.
If in doubt about the correct tyre pressure for the type of work being carried out, contact the manufacturer or your tyre dealer.
Avoiding tyre damage
It is paramount that the two front wheels are parallel or have a slight toe-out. This will help prevent irregular shoulder wear and maximise efficiency.
Pressures and Loads
Ensuring tyres run at the correct pressure is one of the easiest maintenance tasks you can carry out and it will have wide ranging benefits. It will ensure even tyre wear, prevent cracking, provide protection against impact and assist long life.
In terms of overall performance, it will maximise fuel usage, minimise compaction and ensure a comfortable ride for the driver.
All these factors will have an impact on cost. Regular pressure checks and adjustments for field and road work will help you get the most from your tyres, but it is critical when you have just had a new tyre or rim fitted, a new valve or a puncture repaired.
Valves are cheap, but the consequences of deflation are not, so always fit a new one when you change tyres or rims.
Do not exceed the maximum load or speed ratings and aim for the correct power to weight distribution. For standard 4WD work, tractor gearing should be set up to distribute power 35:65 front to rear and weight at 40:60.
Rims
Ensure that the tyre is the correct size for the rim. Even a slight mismatch can result in poor traction, irregular wear, sidewall cracking, bead damage or rim slip.
In extreme cases complete loss of fitment can occur once the wheel is put under load, such as heavy cultivation work, for example.
Flange roll-over is a visible sign that the tyre is too large for the rim or has been incorrectly fitted. Bead damage or chafing indicates the presence of rim slip.
Regularly check rims for signs of cracking, corrosion or damage. Pressure loss may well be gradual, but it will become a persistent problem if left unchecked.
Ensure all wheel nuts are in place and tight. It is also a good idea to keep them lightly greased in case the wheel needs to be removed. A shorn stud is a big inconvenience and a lost wheel can be catastrophic.
Replacing worn tyres
Although it is tempting to squeeze every last penny from your tyres, badly worn rubber is a false economy. Not only can they be illegal and prone to blowouts, but they can end up costing you more in lost performance, particularly traction and handling.
Rubber is perishable and can degrade, so you should consider replacing tyres that are over five years old, even if they have tread remaining.
Think carefully before considering used tyres. Modern tyres are a complex series of components and layers and although the tread may seem sound, you will not know the condition of the structure and carcass and whether it has been subject to abuse or damage.
Never mix bias and radial tyres on the same axle or different tread patterns. Radial tyres have a longer tread life than bias-ply tyres.
What to look out for
Following the above advice will minimise the likelihood of problems, but it is good practice to look out for damage and to get it checked by a tyre professional.
If caught early enough, some damage can be repaired. Left unchecked, costly problems will occur. A puncture in the field is an inconvenience, but a blowout at speed on the road can be life threatening.
Look for cracks, cuts, missing chunks and bulges. There should be no canvas, wires or other material visible.
Sidewalls are often the most vulnerable parts of the tyre because they are exposed and do the most flexing.
Particular care should be taken when near kerbs, entering narrow gate openings or in tight turning circles with machinery or trailers attached to the rear.
Other indications of tyre problems – besides the visual ones – can be observed in terms of performance. Slow punctures should be treated as soon as possible.
Road hop, skipping, rapid or irregular wear are all signs of a problem.
Essential tyre checklist
- Check the track width to ensure the wheels are parallel.
- Radial run-out – the tyre being “out-of-round” – normally a manufacturing fault.
- Pressure checks are one of the easiest tasks you can carry out and will have wide ranging consequences.
- Tread base creasing/cracking – damage where the lug meets the tyre surface, usually caused by overloading/under inflation and very high torque loading of the lugs, on hard surfaces, eg roads.
- De-lamination – where a thin layer of rubber peels back slightly from the tread area. Looks unsightly, but is normally only a cosmetic.
- Bead damage – where the tyre meets the rim. Often caused by poor fitting or mismatched tyres/rims.
Always remember to check any measurements and pressures with your machinery dealer and tyre manfucturer.